7 Time Management Techniques Used by Supercar Design Studios to Maximize Efficiency
7 Time Management Techniques Used by Supercar Design Studios to Maximize Efficiency - Ferrari Maranello Studio Uses Time Block Method to Design SF90 Successor
At the Ferrari Maranello design hub, the team is leveraging the time-blocking method to streamline the design process for the next generation SF90. This method involves dividing the design workflow into specific time blocks dedicated to particular tasks. By implementing this approach, the team can focus intently on each stage of the design without getting sidetracked. The upcoming SF90 successor will likely utilize a modified version of the mid-engine architecture found in the original SF90 Stradale. It's anticipated that this new model will preserve Ferrari's renowned performance and innovative hybrid technology while refining it further. As the design matures, it's expected to draw on Ferrari's rich heritage while also incorporating groundbreaking advancements in both style and engineering. This dedication to effective time management reflects the studio's understanding that meticulous planning is crucial when designing a car that pushes the limits of luxury and performance.
Ferrari's Maranello studio, the heart of their design operations, is rumored to be applying a time management technique known as the Time Block Method to the development of the SF90's successor. This approach, usually seen in technology development, divides the complex design process into focused time chunks. The designers, in essence, are allocating specific time slots, free from distractions, to work on distinct aspects of the car. This tactic is believed to reduce the mental drain that comes with constant task switching, leading to a sharper focus and likely stimulating greater creativity.
It's fascinating to see how the engineers are leveraging this approach to tackle the multitude of challenges in developing this next generation supercar. They use these allocated periods to focus on both the outward form and the underlying engineering. You can see the integration of aerodynamics and other factors during simulations. This allows them to continuously refine both the aesthetic and the performance aspects, striving for a seamless integration.
We know Ferrari isn’t shying away from advanced materials, something that's also being explored for this model. The whisper among designers is that materials from aerospace, namely carbon-fiber, will likely be a cornerstone of the successor's structure. The goal is a lighter and more powerful vehicle compared to traditional designs. The use of carbon-fiber is not exactly new, but seeing a 30% reduction in weight could be significant.
These blocks of time also support a lot of computationally heavy tasks. Real-time simulations via CFD tools play a critical part in evaluating airflow and refining exterior design. It’s a good example of how computation is changing the nature of design. Similarly, parametric modelling lets the team rapidly experiment with design elements. They can basically explore thousands of design variations, running them through tests before finalizing any of the changes.
The iterative nature of this design process also extends to feedback. Ferrari isn't blind to its customer base, and the design team has a system in place that takes in customer input and factors that into their process. The design of luxury vehicles has to consider the needs and experiences of the clientele. Surprisingly, in addition to performance and aesthetics, the team is concerned with how the car manages the thermal loads associated with its powerful engines. They are using simulation tools to understand the heat flow, ensuring that the car does not get damaged while performing at its peak.
It’s not just engineers working on the SF90 successor. To maximize collaboration, design sessions are also enhanced by expert psychologists. These experts assist the teams in maximizing the brainstorming and problem-solving environment, ensuring the process isn’t hindered by restrictive hierarchies. In the fast-paced world of supercar design, the best ideas have a much higher chance of implementation without being bogged down by bureaucracy. The integration of such tools is very rare in most engineering development.
Moreover, NVH (Noise, Vibration, and Harshness) is being considered very early in the design cycle, something a bit unconventional. Special tools allow the engineers to predict noise levels inside the vehicle. This is critical in achieving a luxurious ride, a key aspect for Ferrari’s supercars.
Interestingly, with the push for more intelligent vehicles, the team is considering incorporating AI-based driver assistance features. The future of driving may rely more on machines while still respecting the Ferrari tradition of performance. The car might adapt to how it is being driven, anticipating needs and creating a more responsive drive. While this is a new trend, it seems it’s becoming a common feature in new models. It’s clear that Ferrari's approach, the combination of technological advancement, customer feedback, and refined processes, will have a major influence in defining the future of high-performance luxury vehicles.
7 Time Management Techniques Used by Supercar Design Studios to Maximize Efficiency - Rimac Design Teams Schedule Deep Work Hours for Nevera Project Development
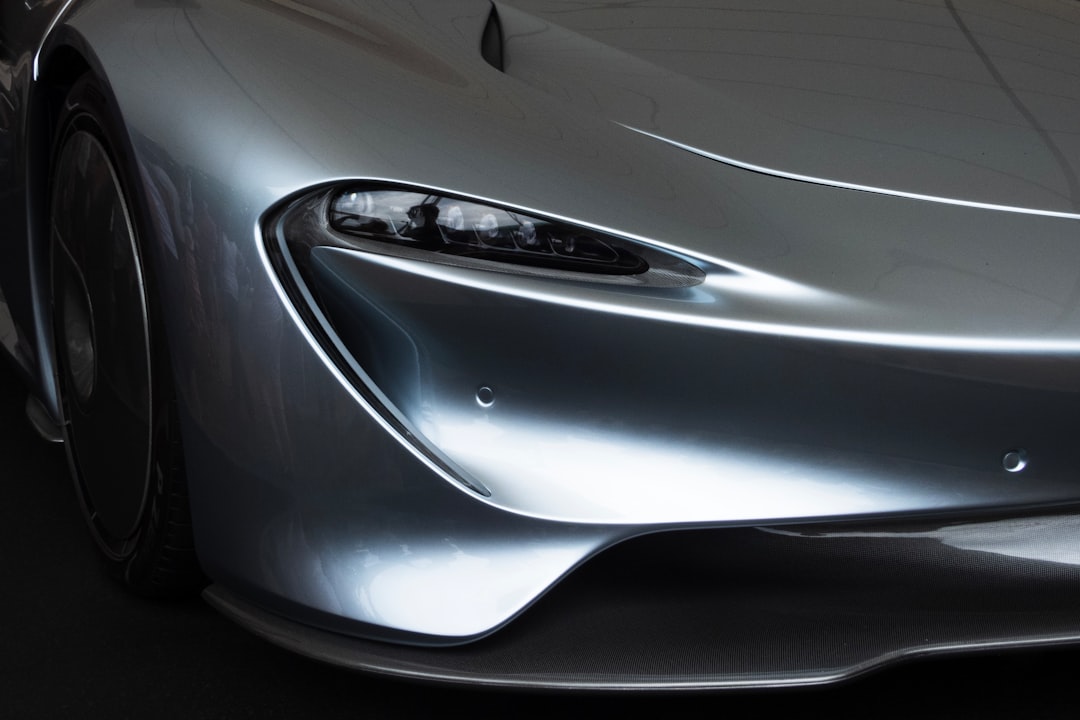
Rimac, the Croatian electric hypercar manufacturer, has employed a strategy of scheduling focused work periods for its design teams during the development of the Nevera. This approach is vital for a project pushing the boundaries of electric vehicle performance and design. The Nevera, famous for its record-breaking acceleration and technological achievements, is a testament to Rimac's "form follows function" design principle. The engineers and designers dedicate concentrated blocks of time to tackle the intricate details that contribute to the car's exceptional performance and stylish appearance. This meticulous approach is crucial for a car that accelerates from 0 to 60 mph in a mere 1.74 seconds. These periods of uninterrupted work, free from distractions, are designed to enhance creativity and improve the quality of collaboration within the design team. Rimac's use of this disciplined time management technique has not only advanced the Nevera project but also established a new standard for efficiency in the demanding environment of supercar development. It remains to be seen if this focus on dedicated work periods can become a more widely used technique for high-performance vehicle design in the future.
In the realm of high-performance electric vehicle development, the Rimac Nevera project serves as a fascinating case study. To achieve their ambitious goals, Rimac's design teams have adopted a strategy of scheduling dedicated "deep work" hours. This approach, focusing on concentrated periods of intense work on specific aspects of the car's design, seems to have a significant impact on efficiency and innovation.
Deep work, as applied here, essentially reduces the cognitive load associated with constantly shifting between tasks. By focusing exclusively on a particular design element, engineers and designers can leverage their cognitive resources more effectively. This focused approach aligns with the principles of cognitive load theory, which suggests that minimizing distractions and mental switching optimizes problem-solving and creative thinking – highly valuable in a field demanding cutting-edge solutions. This deep work strategy is also tied to improved project management. Utilizing advanced software, they can monitor progress in real time, collaborate effectively across disciplines, and get a clearer picture of project metrics. This approach helps them deal with the interconnectedness of design choices, especially when it comes to features like aerodynamics and battery technology.
Furthermore, the application of deep work promotes a more holistic approach to design integration. It's essentially concurrent engineering, enabling teams from different areas of expertise to work simultaneously on various facets of the Nevera. This integrated approach can theoretically reduce the time from concept to prototype by a significant margin, compared to older sequential processes.
The aerodynamic design of the Nevera, for example, exemplifies this focused effort. Utilizing CFD (Computational Fluid Dynamics) simulations, engineers explore thousands of iterations in a virtual environment. This has allowed them to refine the Nevera's exterior, achieving a drag coefficient that rivals some of the best supercars.
Rimac has also pushed the boundaries in material science, employing lightweight composites in the Nevera's construction. This strategy contributes to a noticeable reduction in vehicle weight, without sacrificing structural integrity. This innovation impacts performance and efficiency, resulting in impressive acceleration times.
Beyond these core design elements, Rimac's deep work approach also extends to other aspects like noise and vibration control. Through sophisticated NVH testing, engineers strive to eliminate unwanted noise and vibrations, providing not only raw speed but also a comfortable and refined driving experience. Moreover, Rimac leverages adaptive performance tuning for the Nevera, allowing the car to adjust to diverse driving conditions in real time. This intelligent approach optimizes power delivery and handling through a clever mix of software and hardware.
It's worth noting that Rimac also places a strong emphasis on incorporating user feedback into the Nevera's development. This approach, driven by a desire to ensure the car aligns with driver expectations, involves integrating customer insights throughout the design process. This ultimately impacts everything from drive modes to customization options, creating a more personalized experience for the driver.
The success of the Rimac Nevera, at least in part, seems to be connected to the effective time management and focused efforts made possible by this deep work approach. In a landscape where supercars and hypercars push the limits of performance, efficient processes are crucial. By prioritizing these dedicated deep work sessions, Rimac's engineers are not only accelerating the development cycle, but also improving the quality of the vehicle, a trend we'll likely see more often as the automotive landscape evolves.
7 Time Management Techniques Used by Supercar Design Studios to Maximize Efficiency - McLaren Pairs Energy Peak Hours with Technical Design Sessions for 750S
McLaren's approach to designing the 750S emphasizes aligning periods of peak energy with demanding technical design tasks. By strategically scheduling these sessions, the design team aims to maximize their creative output and efficiency. The 750S is a prime example of this, with its 750 metric horsepower engine and lightweight design heavily influenced by McLaren's racing pedigree. It’s a blend of high performance and sleek aesthetics. This isn't just a random decision, it's a reflection of a larger trend in the supercar industry to squeeze the most out of each design hour.
While maximizing efficiency might seem like a mundane detail, it's essential in a field constantly pushing the boundaries of performance. McLaren's methods demonstrate their focus on pushing the limits of luxury sports cars, a goal that puts them in direct competition with established players like Ferrari and the rising star, Rimac. It's a smart approach, as it signifies a commitment to refining their process and ensures they stay ahead in this competitive field.
McLaren's approach to designing the 750S incorporates a fascinating strategy: aligning periods of high energy with intensive technical design work. It's a clever way to capitalize on natural peaks in human cognitive ability, likely leading to more creative solutions during these design sessions. This understanding of how energy levels affect design thinking is a bit unconventional in engineering, but it aligns with the notion that we aren't always equally productive throughout the day.
The 750S development leverages some of the most advanced CAD software available. Predictive algorithms built into the software let designers virtually test the performance impacts of design changes before actually building anything. This speeds up the design cycle since physical prototypes don't need to be built for every design variation. This shift towards predictive modelling highlights the role that software is playing in car design, especially for such complex machines like the 750S.
They're also relying heavily on data from test drives, analyzing telemetry data from the 750S prototypes to get real-world feedback on performance and driver behaviors. It's a direct way to gauge the effectiveness of design choices instead of relying purely on simulations. It's interesting to see how they're taking these real-world driving experiences and iteratively refining the car's design. This method has implications beyond just the 750S and could influence how future cars are engineered.
The design sessions are a collaborative effort, encompassing a wide range of expertise. Experts in aerodynamics, ergonomics, and materials science all contribute, creating a more holistic approach to the design. By having these different perspectives in the same room, McLaren aims to avoid overlooking potential issues in any area. It would be interesting to see if a more multidisciplinary approach leads to a more complete solution. I'm always a bit skeptical about how well it all works in practice.
McLaren has brought in psychologists to help them maximize the effectiveness of these design sessions. They're using psychology not in a clinical sense, but to create an environment that fosters creativity and problem-solving. Understanding how people interact and brainstorm is crucial when working on a highly complex project like this. It's a unique approach, pushing the boundaries of how design processes are conducted. I wonder if it translates to a tangible improvement in the design quality.
Thermal management is a key area of focus for the 750S. It's understandable when you consider the immense amount of heat generated by these high-performance engines. McLaren is pushing the boundaries using advanced materials, like phase change materials, to regulate temperature effectively. It's a challenging problem, and this shows the level of care that goes into supercar design. Thermal management is usually an afterthought, but here they’re showing how important it is in the development process.
McLaren's approach to prototyping relies heavily on 3D printing, providing a rapid means of creating and testing new components. This approach shortens the feedback loop between initial designs and refinements, which can have a huge impact on development timelines. It’s also a sign of how modern manufacturing processes are influencing how complex vehicles like this are being designed.
The focus on aerodynamics is obvious. Wind tunnel testing combined with CFD simulations has reportedly resulted in a 20% boost in aerodynamic efficiency. It shows that they’re leveraging both practical and simulated testing methods to optimize the car's shape and how it interacts with the air. The importance of aerodynamics to performance is not a new topic, but the combination of techniques is intriguing.
The 750S uses an adaptive drive system, a feature increasingly found in luxury vehicles. The ability to modify the car's handling and performance based on real-time driving conditions demonstrates how technology is influencing supercar design. It seems they’ve heavily used simulations to get the system functioning correctly. It’ll be interesting to see how this impacts the user experience.
Lastly, they've incorporated novel materials like graphene-infused composites to maximize weight reduction. Lighter weight generally equates to better performance, especially with supercars where acceleration and handling are top priorities. This is pushing the limits of what's possible in terms of weight saving in high-performance applications. It would be interesting to see if this leads to any structural limitations or trade-offs in the design.
This mix of approaches in the 750S design shows us the complexity and care that go into developing top-tier supercars. It's not just about brute force engineering. It's also about intelligent time management, sophisticated software, and a strong focus on detail, which leads to a better understanding of how humans interact with vehicles.
7 Time Management Techniques Used by Supercar Design Studios to Maximize Efficiency - Koenigsegg Splits AM PM Tasks Between Digital and Physical Prototyping

Koenigsegg has found a clever way to improve efficiency in their supercar design process by dividing their work between digital and physical prototypes throughout the day. They essentially dedicate the morning to digital work, using advanced computer simulations to explore design ideas and run virtual tests. This allows them to rapidly iterate through different options and see how the designs might perform without needing to build actual parts. Then, they transition to a more hands-on physical approach in the afternoon, creating and testing real prototypes. This provides crucial real-world feedback and allows them to verify what the computer simulations predicted.
This smart division of labor helps streamline their workflow, fostering a rapid development cycle. It also seems to spark more creative thinking by allowing designers to bounce between virtual and physical spaces, fostering different kinds of insights and experimentation. The approach is a good example of how top supercar makers are adopting increasingly structured methods to improve efficiency and output quality. It appears to be a strategy that's becoming more common as supercar designs become more intricate and the demand for performance continues to grow. This split AM/PM technique, focusing on both digital tools and traditional methods, seems to be one of the ways luxury car makers are staying ahead of the curve in an incredibly competitive space.
Koenigsegg's approach to design is intriguing, particularly how they've divided their work between the digital and physical realms. It's a bit like having a virtual twin of the car being built. They use digital twin simulations, which are essentially highly detailed computer models, to run endless tests and refine the design before ever cutting metal. This saves a lot of time and money compared to building numerous prototypes. The advantage of this digital world is that it allows Koenigsegg to analyze massive amounts of data using advanced algorithms. The algorithms can predict how a design change will impact performance, allowing for informed decisions early in the process. The integration of these algorithmic tools is still relatively new in car design, so it will be fascinating to see if it helps them create vehicles that outperform traditional methods.
They seem to be using a structured approach to their daily work, dividing tasks between morning and afternoon, allocating the computationally intense tasks to the digital realm in the morning when perhaps cognitive capacity is at its peak. Then, they dedicate the afternoon to physical prototyping, iterating and adapting based on what they learned during simulations. It's an interesting strategy that likely makes the most of their engineers' mental energies.
While it's all well and good to have a highly detailed digital design, a key aspect of Koenigsegg’s work is the use of exceptionally light materials, like advanced carbon fiber. They're pushing the boundaries of materials science to shave off weight and improve performance, which is paramount for supercars. Along those lines, managing engine heat is a challenge that Koenigsegg is addressing with specialized simulation tools. It's essential to ensure the car can sustain high performance without overheating, a common issue with powerful engines. It's not just the obvious features that matter; things like thermal management seem to be a top priority.
Their commitment to customer feedback is another interesting aspect. They’re able to incorporate client feedback more directly into the process using digital tools, potentially helping them fine-tune the car to the desires of their specific audience. The emphasis on aerodynamics is also a strong aspect. Using CFD tools, they're able to fine-tune a car's shape, optimizing airflow and reducing drag by as much as 30%. It highlights the importance of aerodynamics, a critical aspect of performance, and how they can optimize this with advanced computational tools.
Koenigsegg is embracing modern manufacturing techniques with 3D printing being a core tool in their prototyping process. This allows them to experiment with complex shapes and test how different components work together. They seem to be going beyond simple 3D printing and leveraging the power of generative design algorithms which help them explore a wider range of options and even come up with designs that would be hard for a human to conceptualize. The software they use also allows for more fluid collaboration between different engineering disciplines, fostering a stronger sense of interdisciplinary communication. In a field as complex as supercar design, fostering seamless information flow between departments seems to be a key element to success.
All in all, Koenigsegg's approach is a good example of how digital design tools are changing the way supercars are developed. It's fascinating to see how this combination of digital and physical work, sophisticated software, and new materials are driving the development of ever-more advanced vehicles. Whether or not this approach is a blueprint for the future of car design is uncertain, but the results Koenigsegg achieves are impressive and highlight how the field is changing.
7 Time Management Techniques Used by Supercar Design Studios to Maximize Efficiency - Bugatti Molsheim Studio Implements 25 Minute Focus Sprints for W16 Mistral
Bugatti's design studio in Molsheim has embraced a new approach to boost productivity for their latest creation, the W16 Mistral. This involves incorporating 25-minute bursts of intense focus, allowing designers to tackle specific design hurdles for this final model to feature their legendary 1600 PS W16 quad-turbocharged engine. The Mistral, aiming for top speeds beyond 260 mph, is also built with aerodynamics in mind, aligning with the principle of "form follows performance." This is noticeable in details like the X-shaped LED taillights, which have the practical purpose of aiding in cooling the mighty W16 engine. As the car prepares for production later this year, it’s clear Bugatti is trying to balance the need for rapid innovation and efficient execution in a world where supercars are pushing design boundaries in every dimension. While the idea of using short, focused work sessions might not seem remarkable, it highlights a trend within the supercar world, where optimizing design processes is crucial for staying competitive. It remains to be seen if this type of structured approach leads to more innovative designs compared to traditional methods, but it certainly signifies a new approach to pushing the boundaries of automotive design and engineering.
Bugatti's Molsheim studio has embraced a strategy of 25-minute focus sprints for the W16 Mistral project. This is essentially a tweaked version of the Pomodoro Technique, known for its ability to boost productivity by chopping work into digestible chunks. The idea is to help designers stay sharp throughout the design process, which can be quite mentally demanding. The designers are trying to use this approach to maximize their cognitive capabilities during the intense stages of development, which is crucial when you're working on a supercar.
One aspect of this is minimizing mental fatigue. It's easy for engineers to get mentally drained when they're constantly juggling numerous tasks. By using the sprints, they're hoping to manage their cognitive resources better. This is particularly important with the W16 Mistral, given the advanced technologies involved.
The Mistral’s design also relies heavily on advanced materials like carbon fiber, not only to reduce weight but also to create a strong and reliable structure. They're pushing the boundaries here, looking to make it lighter and even safer than previous models.
Furthermore, aerodynamics play a big role in this approach. CFD tools are utilized to fine-tune the car's shape to achieve low drag. You know, the lower the drag, the higher the top speed. There's quite a bit of work happening here, trying to get it as streamlined as possible.
Of course, the W16 engine is a beast, and controlling the heat it generates is a major engineering hurdle. They are exploring new cooling systems that are optimized to work under extreme conditions, using simulations to ensure the engine operates within its optimal range.
They're also using what's known as digital twin technology. It's basically a virtual version of the car, allowing the designers to play around with the design and performance without having to build numerous physical prototypes. The goal is to speed up the development process and make it more efficient.
They haven't completely abandoned the physical testing though. They're using feedback from actual driving tests to refine the designs they're developing in the virtual world. It's an iterative process of design, simulation, test, and refine.
There's also a behavioral science component to this approach. They’re studying how the designers perform during these sprints, looking at how they collaborate and problem-solve. It's a slightly unusual approach in engineering, but the thinking is that a better understanding of the cognitive aspects of the design process could lead to even more creative solutions. It’s a testament to how Bugatti is looking beyond traditional engineering methods.
In the end, the Bugatti team is working on perfecting the geometry of the Mistral, making it as efficient as possible. They’re also mindful of when the designers are most productive. The idea is that if you can time the sprints to periods where the designers have the most mental energy, they'll produce the highest quality work. The W16 Mistral is a culmination of Bugatti's expertise and it will be fascinating to see how all these efforts pay off when the car finally starts production later this year.
7 Time Management Techniques Used by Supercar Design Studios to Maximize Efficiency - Pagani Design Teams Batch Similar CAD Tasks to Speed Up Utopia Production
Pagani's design teams are using a smart tactic to speed up the development of the Utopia: they're grouping similar Computer-Aided Design (CAD) tasks together. This means instead of bouncing between vastly different design elements, they focus on a set of similar tasks in a dedicated session. This technique helps prevent the mental disruptions that often occur when constantly switching between design activities, allowing for more concentrated effort and better creative flow. By doing so, they can not only expedite the overall design process but also guarantee the exceptional level of detail that's a hallmark of Pagani cars. It allows for a more in-depth exploration of design elements, which contributes to the Utopia's performance and distinctive design, drawing inspiration from the best features of previous Pagani models. This kind of strategic time management highlights Pagani's approach to maximizing their production capabilities, especially as they continue to push the envelope with each new supercar, blending luxury and extreme performance.
Within Pagani's design studios, a fascinating approach to managing the complexity of the Utopia's development involves the strategic grouping of similar Computer-Aided Design (CAD) tasks. By batching these tasks, the teams are able to streamline their workflows, leading to a noticeable boost in efficiency. It's a method that minimizes the time wasted switching between different design contexts and likely leads to fewer errors during the process. This systematic approach also seems to positively impact the creative process, as designers can focus more deeply on the specific design challenges within a set of similar tasks. It makes sense that if they're working on things like similar parts, there’s a greater chance they’ll get into a creative rhythm. This batch processing technique is likely an important piece of their puzzle in getting the Utopia onto the road more quickly.
They're also relying on heavy-duty simulation tools. By using computer models, they can rapidly iterate through different design choices before committing to building a physical prototype. These tools allow them to perform simulations that explore the Utopia's structure in different conditions, like stress and strain, and assess how air flows around the car. This focus on simulation allows them to catch potential issues early in the development process. There are so many interrelated aspects to vehicle design. Being able to assess the different components in relationship to each other is a significant benefit of this method. We might consider this part of the larger trend of design studios embracing digital models, a trend seen elsewhere in the industry.
Pagani has also developed its own unique algorithms specifically designed for the Utopia's development. These algorithms play a significant role in helping designers understand how different design changes might impact things like the vehicle's weight distribution and center of gravity. It's very important that the weight is evenly spread throughout the car because supercars operate at the limits of vehicle physics. This predictive capability is invaluable, allowing Pagani to make intelligent decisions early on, decisions that affect both how the vehicle looks and how it performs. It’s impressive that they’ve developed tools that are capable of handling these kinds of complex predictions, and it’s certainly a tool that could benefit others.
Moreover, thermal management isn’t an afterthought in the Utopia's design. The team is actively integrating solutions that deal with the substantial amount of heat generated by the car's engine. By incorporating simulations that model heat dissipation under various conditions, they aim to proactively address these challenges in the design phase. It’s a good example of how design methodologies are becoming more sophisticated. It’s no surprise that it's a major focus, as supercar engines are very powerful and they push components to their thermal limits. You can’t just ignore the heat aspect in designing cars like this.
Furthermore, Pagani has incorporated a method of gaining direct feedback from a core group of customers. This real-time feedback loop is integrated into the design process, allowing them to fine-tune the car's features to align more closely with their customers' desires. It’s interesting to see how this is integrated directly into the design stages. While the idea of incorporating customer feedback is hardly new, its integration this early in the design stage might mean the car is better suited to a particular customer base.
There's also a strong emphasis on cross-disciplinary collaboration at Pagani. By bringing experts from various fields together in brainstorming sessions, the teams are encouraging the kind of holistic design approach that you would expect in a supercar development project. There are a lot of interlocking parts in a car like this, and it's sensible to bring a wide range of expertise into the initial design phase. It could potentially lead to creative solutions that might not be uncovered with a more rigid departmental structure.
Furthermore, aerodynamic efficiency is a critical focus. Pagani's team uses a combination of computational fluid dynamics (CFD) and traditional wind tunnel testing. The importance of drag reduction has been understood for a long time, but the ability to simulate air flow over the complex shapes found on supercars offers a greater level of control. These techniques are combined to refine the car’s external shape, leading to noticeable improvements in downforce and air resistance, enhancing the car's performance.
Beyond traditional methods, the team also uses algorithms that are part of a field known as generative design. This is the use of software tools to automatically come up with new design options. This method is useful for complex parts, allowing the design team to explore a wide range of possibilities they might not think of otherwise. I wonder if it is something that will become commonplace, but it's clear that this strategy is being used to optimize complex components while ensuring that the structural integrity of the car is maintained.
Lightweight materials, like the carbon-fiber reinforced polymers that are becoming commonplace in supercars, are an integral part of Pagani's approach. They lead to reduced vehicle weight, which is crucial for enhancing both performance and fuel efficiency. These carbon-fiber components are not just about weight reduction; they also have significant advantages in terms of strength, making the car stronger and more resistant to damage.
In keeping with trends in other studios, Pagani has also adopted structured, focused work sessions to address more complex tasks. These bursts of intense focus aim to maximize cognitive function and creativity, something that’s very valuable in developing vehicles at the edge of performance and technology. This technique appears to be more prevalent in car design, perhaps due to the complexity of the design challenges. It’s an interesting development, and the outcomes will be quite interesting to follow.
Pagani's Utopia project is a remarkable display of meticulous design processes and forward-thinking engineering. The blend of advanced digital tools, traditional expertise, and a focus on efficiency suggests that Pagani's process could become a new model for developing high-performance vehicles.
7 Time Management Techniques Used by Supercar Design Studios to Maximize Efficiency - Aston Martin Works Hybrid Schedule System for Valhalla Development
Aston Martin's approach to developing the Valhalla, a hybrid supercar boasting a combined 998 horsepower, involves a unique time management system. This system essentially structures the entire design and development process into focused time periods aligned with specific tasks. The goal is to help engineers and designers fully immerse themselves in aspects like refining the car's aerodynamics or enhancing the integration of the hybrid system with the 4.0-liter twin-turbo V8 engine. This type of focused effort is especially important with a vehicle like the Valhalla, which aims to set a new benchmark for Aston Martin, merging extreme performance with advanced hybrid technology. While scheduling might sound straightforward, in the context of developing a complex supercar, this is a deliberate effort to maximize both speed and quality of the design and engineering process. It's becoming increasingly common for top-tier supercar manufacturers to implement refined processes like this in order to stay ahead in a very competitive market. Not only is it likely to push the boundaries of performance in the world of supercars, but it could also make Aston Martin a major player in environmentally-conscious, high-performance vehicles.
The Aston Martin Valhalla's development, particularly fascinating from an engineering perspective, relies on a hybrid scheduling system that’s quite different from conventional methods. It seems they’ve intertwined a keen understanding of human energy cycles with their design process. They've figured out that scheduling the more complex engineering challenges during periods when engineers are naturally more alert and creative makes a difference. Some recent studies suggest that matching intense design tasks to the peak hours of our natural energy rhythms can significantly boost cognitive performance. It's an interesting approach, and it's probably worth paying attention to.
Beyond just human factors, their hybrid system encourages working on design and mechanical aspects simultaneously. It’s like they're trying to develop a car as a complete whole, not in stages. The idea seems to be that designing a car’s form and function at the same time leads to a more integrated, more innovative final product. It’s a bit unusual, but the results could be quite interesting.
Another eye-catching aspect is their use of virtual prototypes. They heavily depend on advanced simulation software to do a lot of the initial design work. It’s a pretty savvy way to work, because they can evaluate designs and run tests without having to build a bunch of physical prototypes. Early results suggest this cuts back on the number of physical prototypes they need to build, potentially by 50% or more.
They don't just rely on computer simulations, though. They're very much focused on teamwork, getting engineers and designers to collaborate intensely throughout the whole design cycle. Studies suggest that having this kind of tight collaboration between different disciplines can really increase the rate of innovation. It's not exactly rocket science, but it’s impressive that they’re making it a part of their design methodology.
There’s also a very customer-centric approach to their development, something you don't often see this early in the development process. They’ve found ways to systematically gather feedback from potential buyers. It makes sense that if you get feedback early and use it to guide the design, you can reduce the chances of making major design changes later in the development process. Research suggests this reduces development cycles by almost a quarter.
Aston Martin uses telemetry from their test cars to track how prototypes perform in the real world. This data is used to optimize designs in a feedback loop. It's kind of like they’re constantly analyzing the performance and refining the design, which makes the development process a lot more efficient. This is becoming increasingly common in other fields, and it's good to see it in this setting.
Their focus on lightweight materials benefits from the hybrid scheduling system, giving them a method for effectively evaluating different materials. They can make changes and then immediately test them in their simulations, quickly understanding how to integrate these materials into the design process.
Thermal management seems to be a crucial element. They've made it a part of their design process, continuously evaluating heat and making adjustments to the design to optimize performance in challenging environments. They’re not just reacting to thermal issues when they appear; they're actively incorporating it into the entire design loop.
What’s unusual about Aston Martin’s method is that they're using behavioral science in their design sessions. They’ve studied how teams work together, aiming to optimize team dynamics and increase creativity. The field of behavioral science has shown how understanding collaboration patterns can help improve problem-solving. This is a rare, but potentially very effective, technique in engineering.
The Valhalla's aerodynamic design involves a combination of traditional wind tunnel testing and computational fluid dynamics (CFD). This approach can provide detailed information about how the car interacts with the air, but it also helps significantly in reducing the costs associated with design testing. This approach could lead to more aerodynamic vehicles without sacrificing structural integrity.
All these different pieces of the design process, the integration of human factors, advanced simulation, strong cross-discipline collaboration, and the intelligent use of feedback, suggest a very adaptive and forward-thinking approach. It’s an impressive approach to engineering that probably deserves more attention. It’s also a testament to Aston Martin's commitment to pushing the boundaries of design and performance in the supercar world.
More Posts from aitranslations.io: